Mirror welding, a special skill
For making connections between parts of the same or different types of plastic, various methods and techniques are used, such as ultrasonic, flange connection, hot gas welding, wire welding, and extrusion welding. In this blog, we will delve deeper into another technique, namely mirror welding. This is one of the welding methods that we at RKT frequently apply, both in the workshop and on-site.
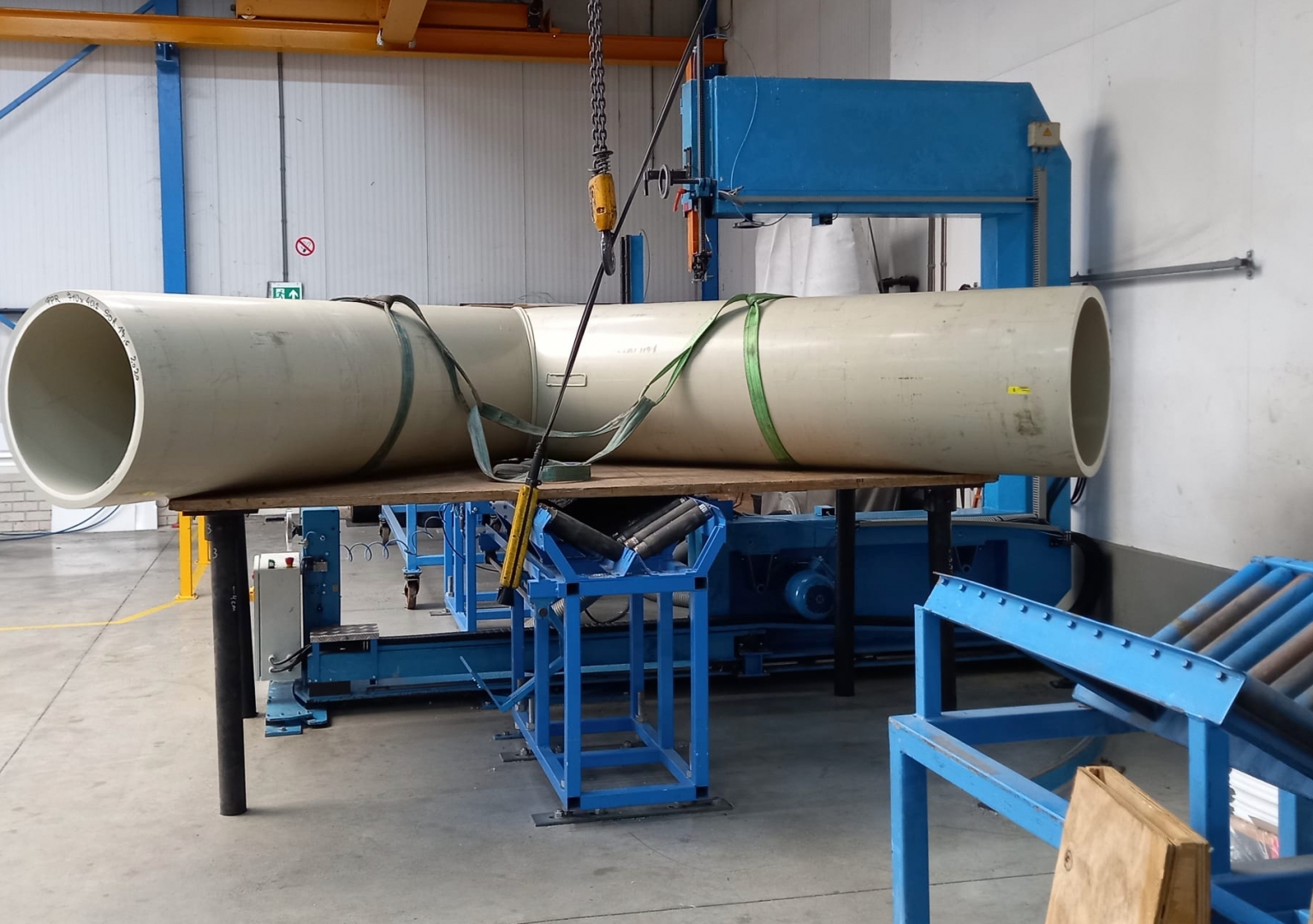
HDPE and PP
What's special about mirror welding is that it's a very reliable, safe, and extremely strong connection technique suitable for small to very large diameters (up to 1400mm!). The technique is particularly used in processing plastics HDPE and PP, especially for sheet material and piping.
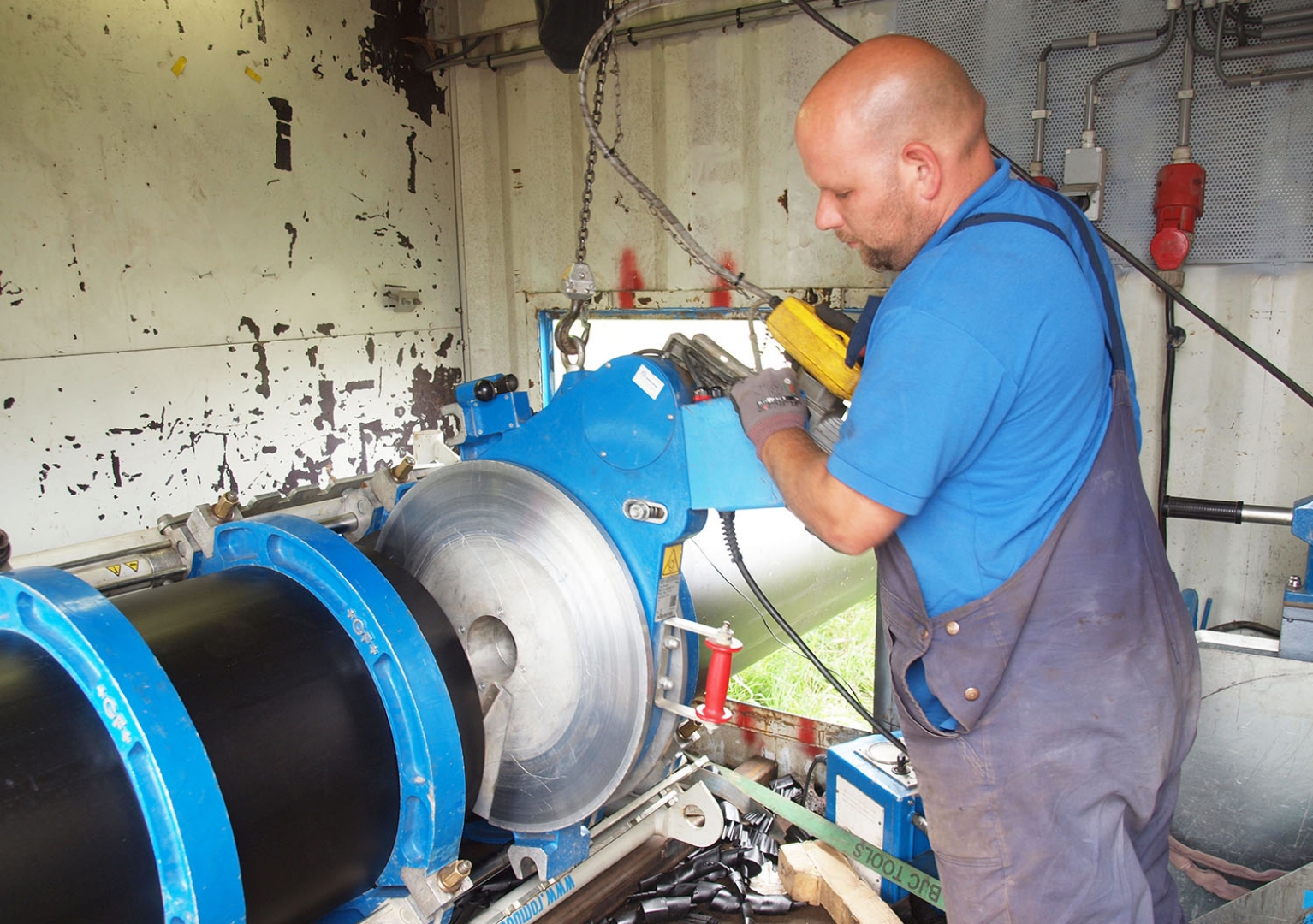
The welding process
In mirror welding (also called butt welding), we heat two welding surfaces, for example, two pipe sections, with a so-called welding mirror. Before we do that, both parts are flattened to make them fit precisely. Then we place the mirror between them. This mirror is a metal plate that is heated to about 210 degrees, which is the melting point of the plastic. Once the welding surfaces are sufficiently heated, the welding mirror is removed and the two parts are pressed together with force.
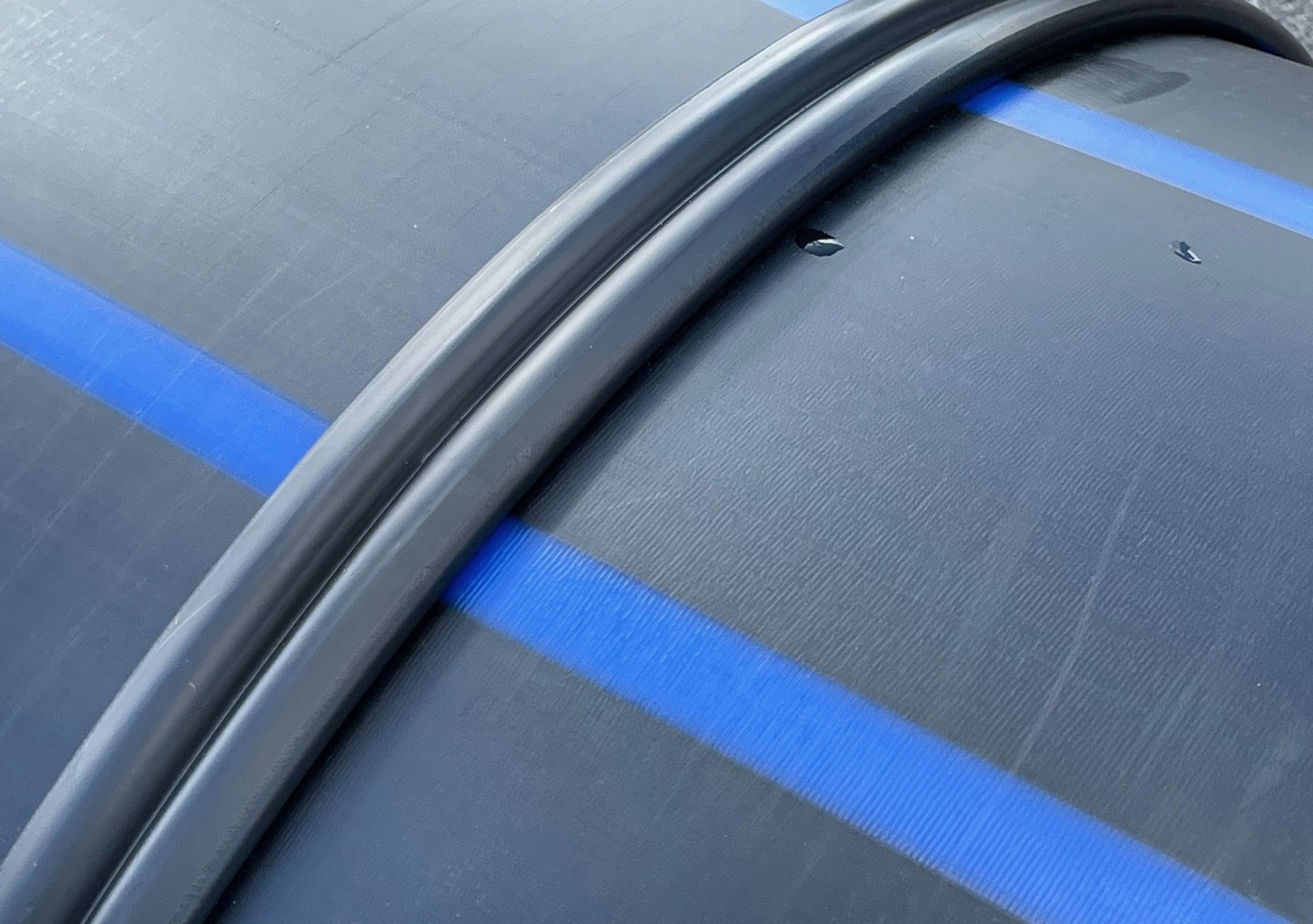
The Bead
During the welding process, a so-called weld bead forms on the inside and outside of the pipe. In some cases, it is desirable for this bead to be removed, for example in casing pipes through which fiber optic or other cables are threaded. A bead remover is used to remove the bead just after the weld is made, when the material is still about 200 degrees.
Mirror welding using a hydraulic welding machine in the workshop
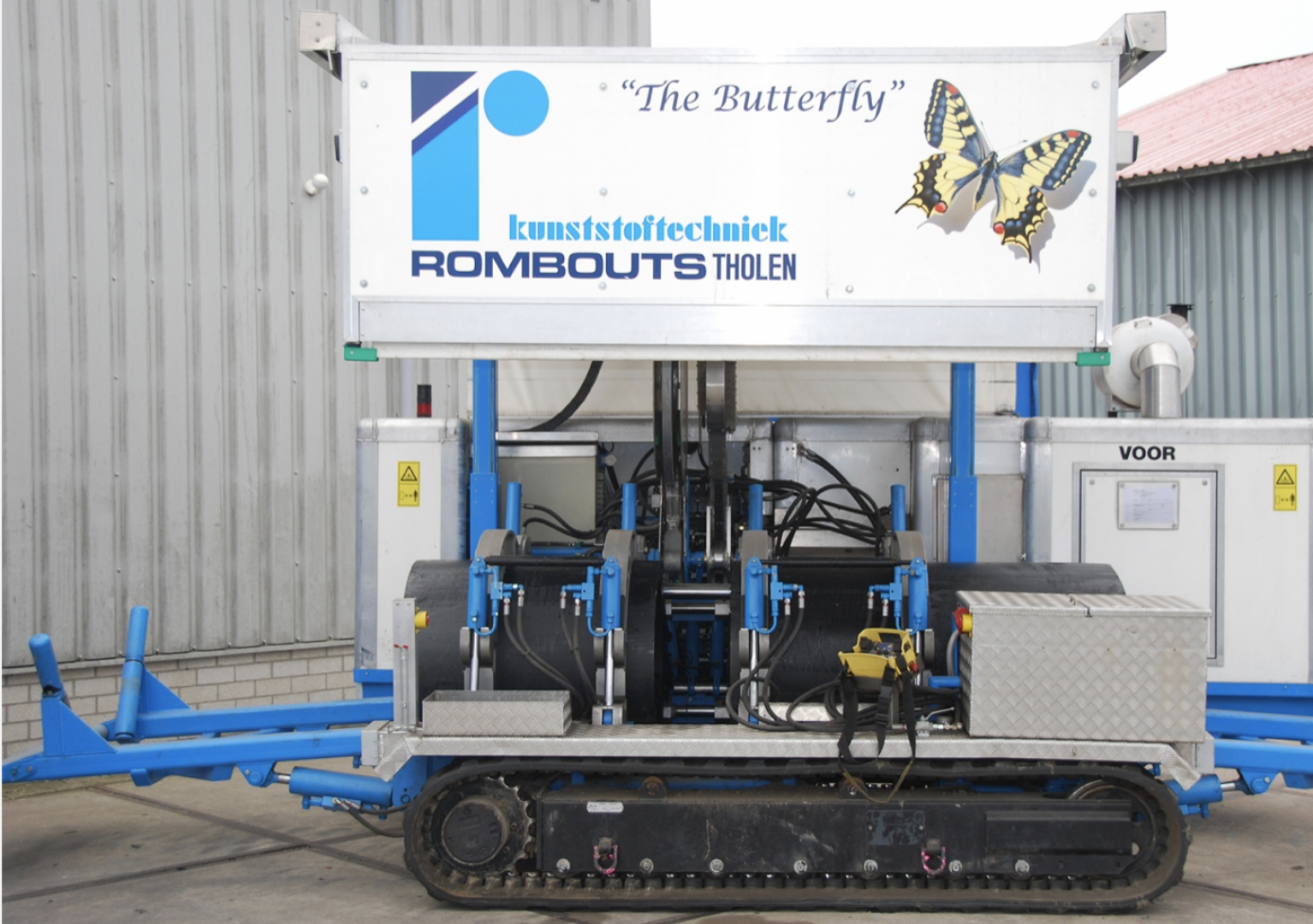
Saving valuable time with the welding machine
The cooling of the weld, depending on the diameter and wall thickness, takes time. This can amount to about 2 hours for a pipe of considerable size. To prevent this valuable time from being lost, we use multiple mirror welding machines. Since we have at least two examples of all mirror welding machines available, the next weld can already be started during the cooling time of the first one. This shortens the turnaround time of projects. The Butterfly and Grasshopper welding machines are mobile welding machines developed in-house, suitable for pipes from Ø 500 to Ø 710.
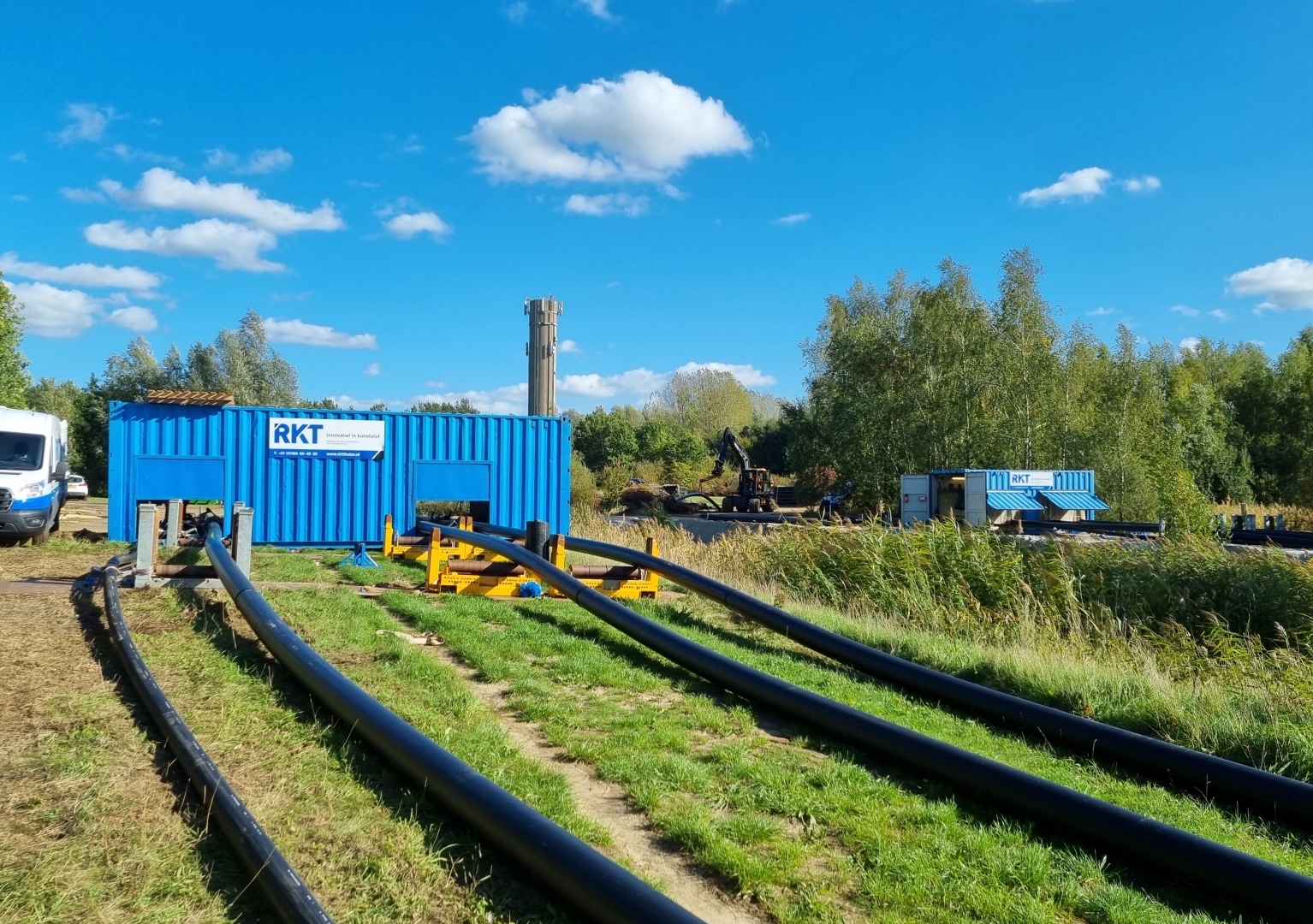
Mobile welding containers
Another way to increase productivity is the use of one or more mobile welding containers. These can accommodate multiple welding machines. In the welding container, the welders have at least two welding machines at their disposal. This allows them to start on the next weld while the previous one is still cooling down.
The Butterfly welding robot in action at the Maasvlakte
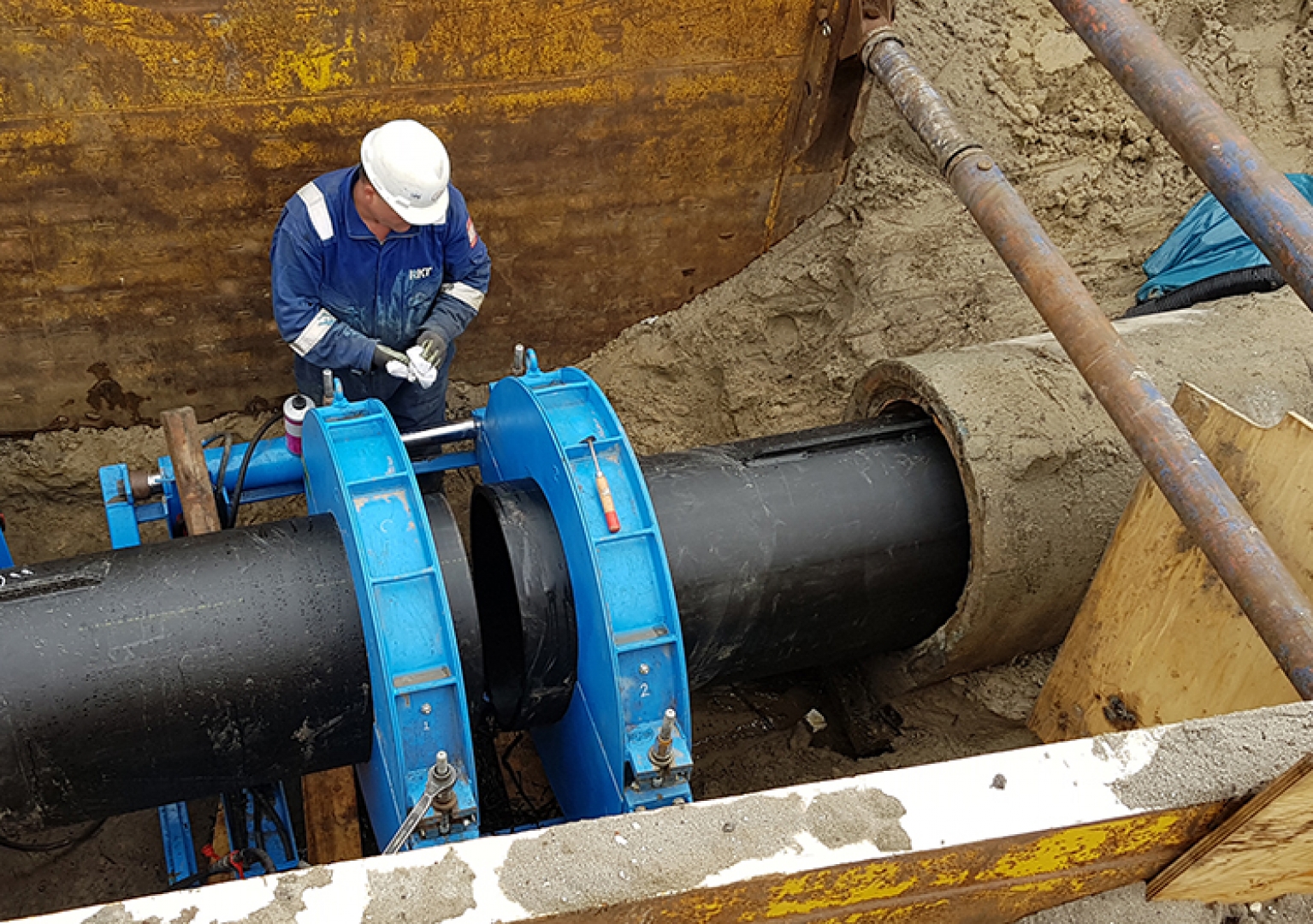
Special shapes
Not all pipes are always round in shape. For example, some sewer pipes are egg-shaped. When these cannot be replaced by open excavation, sometimes the choice is made to slide a plastic liner into the concrete pipe. These liners must, of course, also be egg-shaped. For such tasks, our machines are modified to be able to weld the egg-shaped pipe.
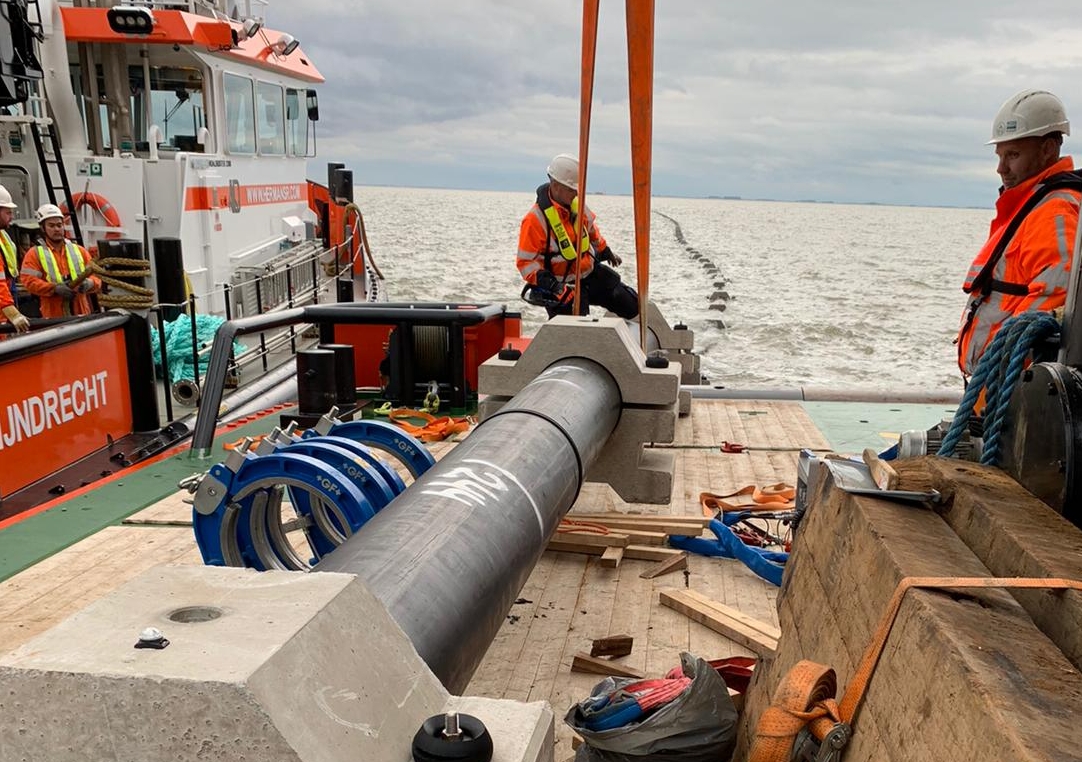
Safe, reliable, and environmentally friendly
Mirror welding is thus a safe and very reliable connection technique for a wide range of diameters. Moreover, no harmful fumes are released during the process. This makes this welding method one of the most environmentally friendly as well.